Trusted Packaging Machine Repair Service for Long-Lasting Equipment Performance
Comprehending the Key Components and Repair Work Methods for Packaging Machine Upkeep
Effective upkeep of product packaging equipments hinges on a thorough understanding of their crucial parts, including the structure, drive system, and securing devices. Recognizing usual maintenance issues, combined with the implementation of preventative approaches and troubleshooting techniques, can significantly boost machine integrity.
Trick Parts of Packaging Equipments
Packaging equipments contain a number of vital elements that interact to ensure reliable and reliable packaging procedures. At the core of these machines is the framework, which gives structural honesty and houses the different operating components. The drive system, often a combination of gears and electric motors, helps with the motion of parts, enabling precise operation throughout the product packaging cycle.
An additional important element is the conveyor system, which moves products through different stages of the packaging process. This is typically enhanced by sensors and controls that keep an eye on the position and rate of items, making certain synchronization and reducing errors. The filling system is vital for precisely dispensing the ideal quantity of product right into bundles, whether in liquid, powder, or solid form.
Securing devices, including warm sealants or sticky applicators, play an important duty in securing bundles, avoiding contamination and extending service life. Additionally, classifying systems are essential for offering necessary product details, making certain conformity with policies. The control panel, geared up with easy to use interfaces, enables drivers to take care of equipment features, monitor efficiency, and make modifications as needed, making certain optimal performance and performance in product packaging procedures.
Typical Maintenance Issues
Efficient procedure of packaging machines counts greatly on normal maintenance to avoid usual issues that can disrupt production. Among these issues, mechanical deterioration is widespread, particularly in parts like seals, conveyors, and electric motors, which can lead to unforeseen downtimes. Additionally, misalignment of components can result in ineffective operation, triggering items to be improperly packaged or damaged throughout the process.
Another typical upkeep concern involves the accumulation of dust and debris, which can hinder the device's sensing units and relocating components. packaging machine repair service. This not just influences performance but can likewise pose security threats. Lubrication failures can lead to raised rubbing, resulting in getting too hot and ultimate part failure.
Electrical issues, usually originating from loose links or worn-out circuitry, can interrupt equipment functions, resulting in substantial production hold-ups. Finally, software program problems because of obsolete programs or incorrect setups can hinder the equipment's operation, necessitating instant intervention. Resolving these common upkeep issues proactively is important for making sure optimum performance and long life of product packaging machinery.
Preventative Upkeep Techniques
Implementing preventative maintenance methods is important for maintaining the efficiency and integrity of product packaging makers. These approaches encompass a methodical technique to maintenance, focusing on the routine evaluation and servicing of tools to preempt prospective failures. By sticking to a scheduled maintenance program, operators can determine damage on parts before they result in considerable failures.
Crucial element of a preventative upkeep strategy include regular assessments, part, cleansing, and lubrication substitutes based on manufacturer recommendations. Making use of checklists can improve this procedure, guaranteeing that no vital jobs are ignored. Furthermore, preserving precise records of upkeep tasks help in tracking the equipment's efficiency with time, helping go to the website with notified decision-making pertaining to future maintenance needs.
Training personnel on the importance of preventative maintenance improves conformity and cultivates a culture of proactive treatment. Implementing an anticipating maintenance component, utilizing information analytics and sensor modern technology, can further enhance equipment performance by predicting failures before they occur.
Repairing Techniques
When faced with malfunctions or inefficiencies in packaging machines, using organized troubleshooting strategies is crucial for identifying and settling concerns swiftly. The very first step in effective troubleshooting is to establish a clear understanding of the equipment's operational criteria and efficiency metrics. This includes examining the equipment's specifications, along with any kind of error codes or alerts shown.
Next, drivers ought to carry out a visual assessment, looking for evident indicators of wear, damage, or imbalance. This typically consists of checking out sensing units, belts, and equipments to pinpoint potential root causes of breakdown. Gathering operational data, such as manufacturing prices and downtime logs, can likewise provide insights right into reoccuring problems.
As soon as prospective issues are identified, using a sensible method to isolate the source is essential. This may need screening individual elements or systems in a regulated fashion. Participating in conversations with operators that engage with the equipment frequently can generate valuable comments about uncommon habits or patterns.

Repair Service and Replacement Finest Practices
A detailed understanding of fixing and substitute ideal methods is crucial for keeping the durability and efficiency of product packaging machines. Frequently analyzing the problem of device parts allows for prompt treatment, preventing even more substantial concerns that can result in pricey downtimes.
When repair services are needed, it is necessary to make use of OEM (Original Equipment Supplier) parts to ensure compatibility and efficiency. This not just protects the honesty of the device however also supports guarantee arrangements. Additionally, it is a good idea to keep an inventory of important spare parts to assist in fast substitutes and lessen functional disturbances.
For intricate repair services, engaging licensed professionals with specialized training in product packaging check over here machinery is recommended. They possess the competence to detect concerns accurately and carry out repair services effectively. In addition, recording all repair tasks and parts replacements is vital for keeping an extensive maintenance history, which can help in future troubleshooting.
Lastly, implementing a proactive approach, including regular inspections and predictive upkeep techniques, improves the dependability of packaging machines. By sticking to these finest practices, businesses can ensure optimal device efficiency, decrease functional threats, and expand equipment life-span.
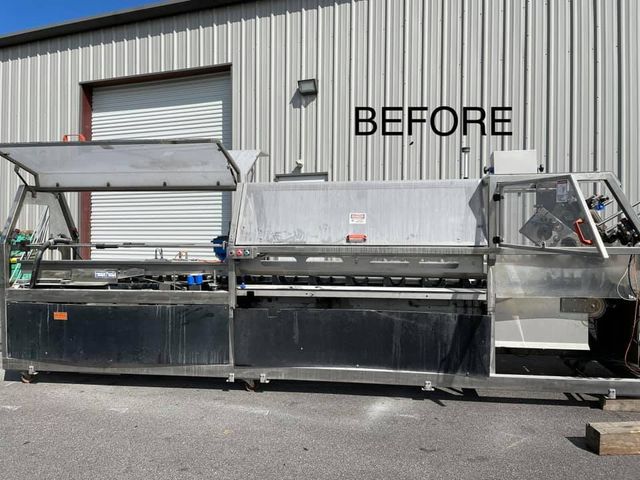
Conclusion
In conclusion, a thorough understanding of product packaging equipment components and important source effective maintenance methods is essential for ideal efficiency. Regular examinations and using OEM components can dramatically reduce downtime, while a well-documented upkeep background promotes positive care. Using certified technicians additionally improves fixing top quality and reliability. By implementing these methods, companies can guarantee the durability and effectiveness of product packaging machines, eventually contributing to improved operational performance and reduced expenses.
Efficient upkeep of product packaging devices pivots on an extensive understanding of their crucial elements, including the framework, drive system, and securing devices.Efficient procedure of packaging machines depends heavily on regular upkeep to prevent typical concerns that can interfere with production.Implementing preventative maintenance methods is important for maintaining the efficiency and dependability of product packaging machines. Additionally, maintaining precise records of upkeep tasks aids in tracking the equipment's performance over time, assisting in informed decision-making pertaining to future upkeep needs.
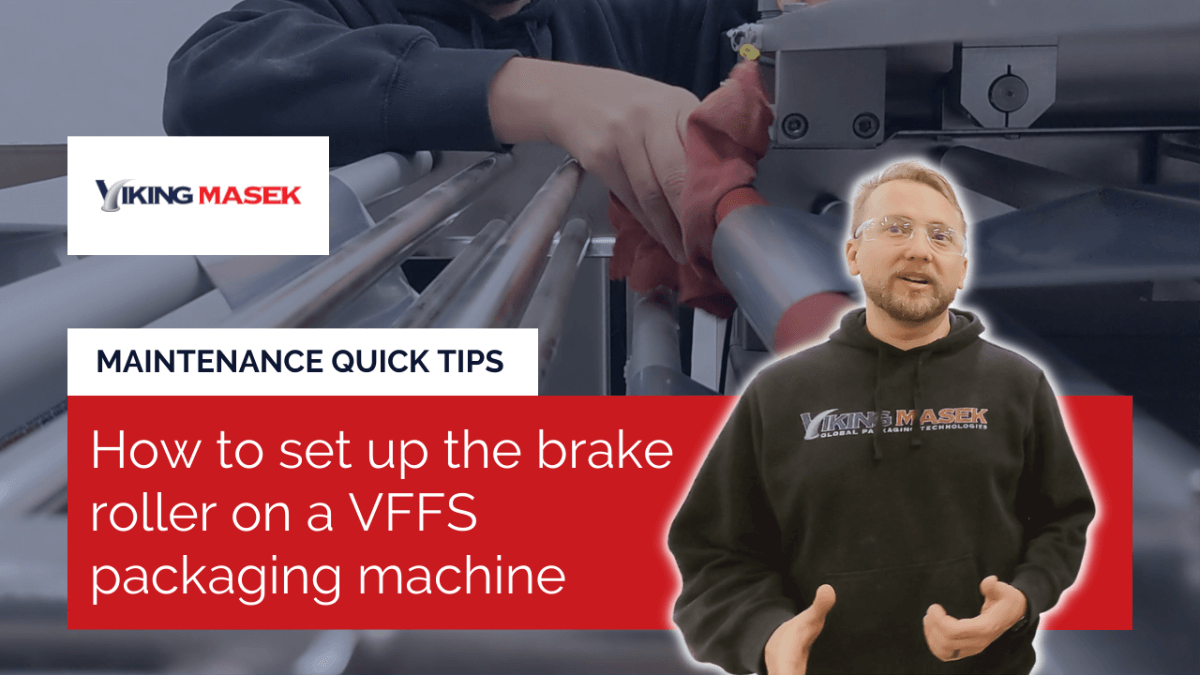